For the past 50 years, InOpera group has been facilitating a direct collaboration between architects and designers in the UK and the product manufacturers in Italy. We’ve noticed, terrazzo material has had a renaissance in the past few years due to its versatility, style, quality and eco-friendliness.
Here we’re discussing everything you need to know about terrazzo specifications and design procedures, specific to the EU standards of production and application.
First, a bit on the history of terrazzo
Modern Terrazzo was originated in Northern Italy, where the biggest marble quarries in Europe are located at. Marble workers of the region would take the crumbs of their work home, mix it with a mortar and made faux stone floors for their terraces.
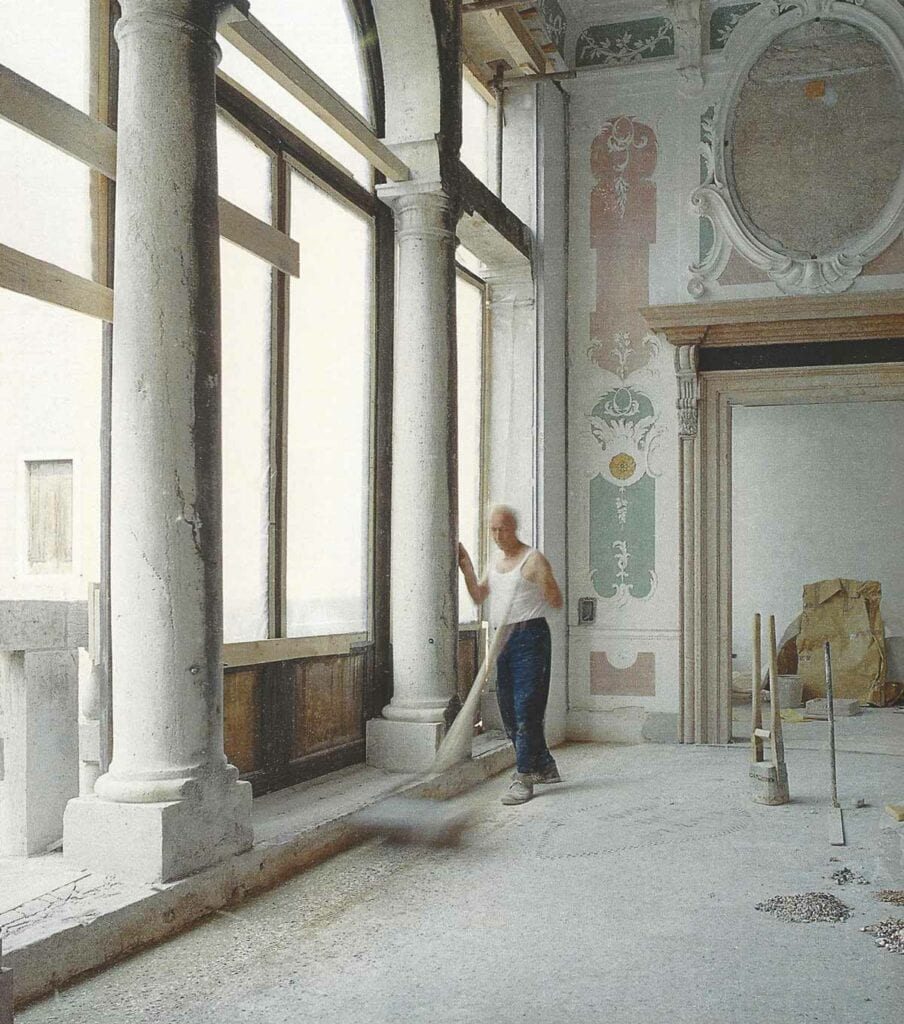
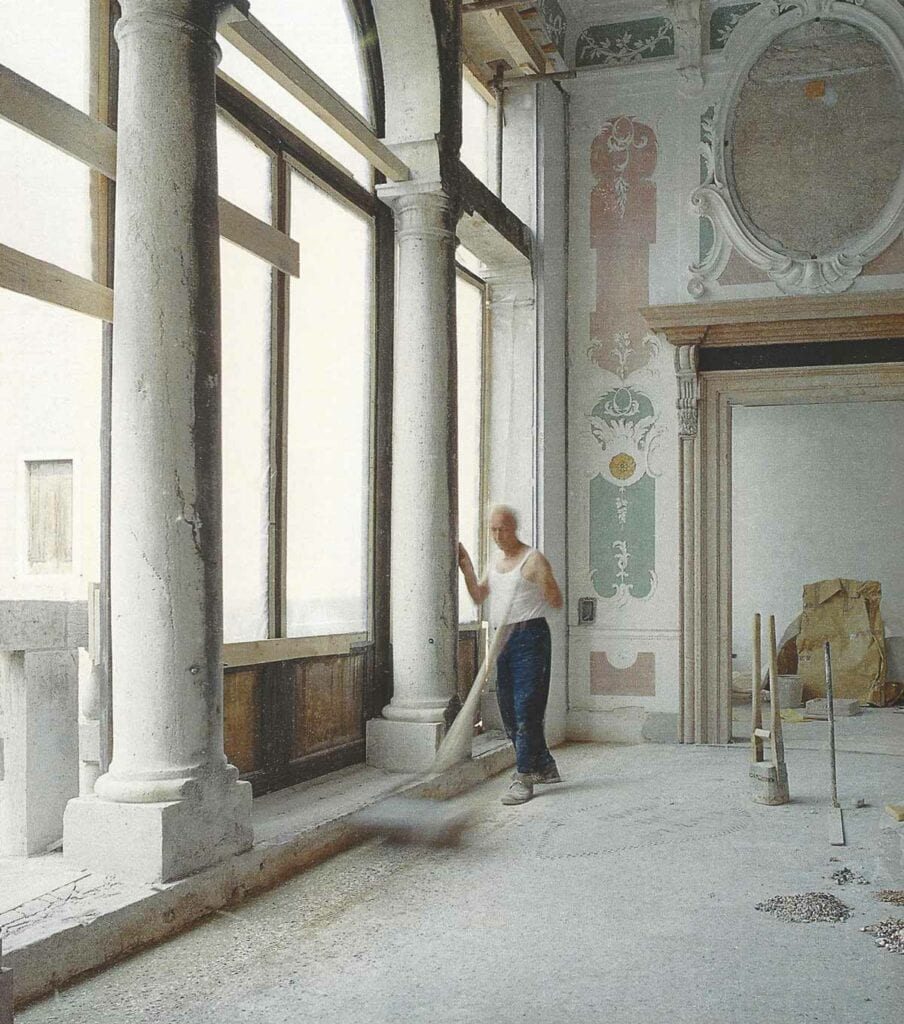
What is terrazzo?
Today, terrazzo essentially is a mix of marble, granite, quartz or glass chips in a binding agent. It offers endless design variations and ease in application, retaining its original quality.
Terrazzo is not just commonly used for indoor flooring, but also for wall surfaces, gardens, facades, finishing panels etc.
When it comes to choosing terrazzo, it is essential to get familiar with the methods and procedures of producing the material to get the most out of the possibilities the material offers.
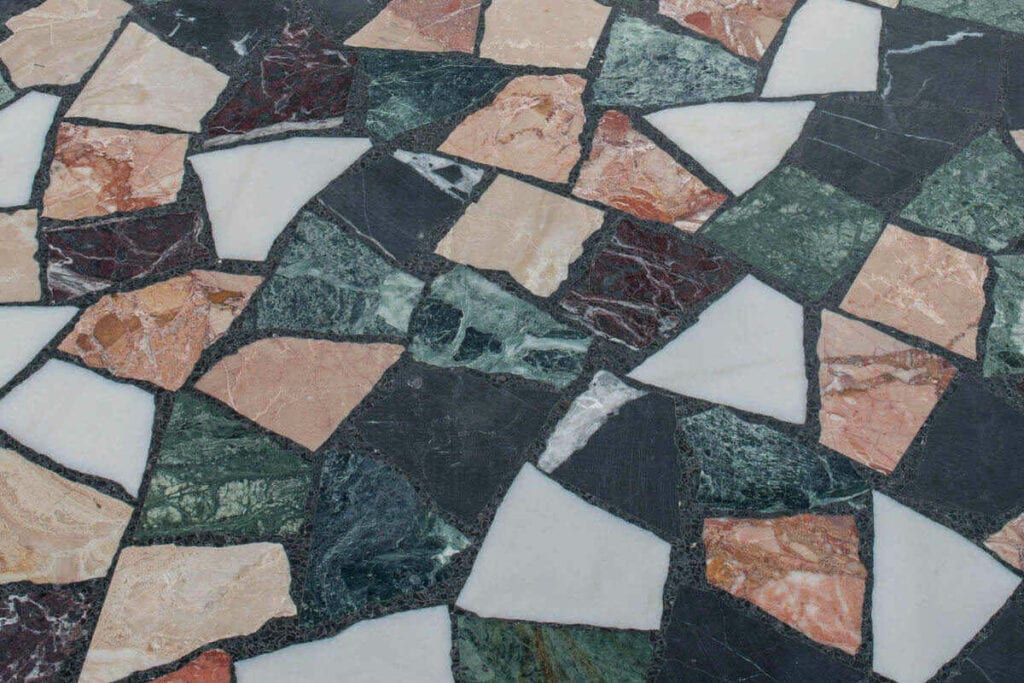
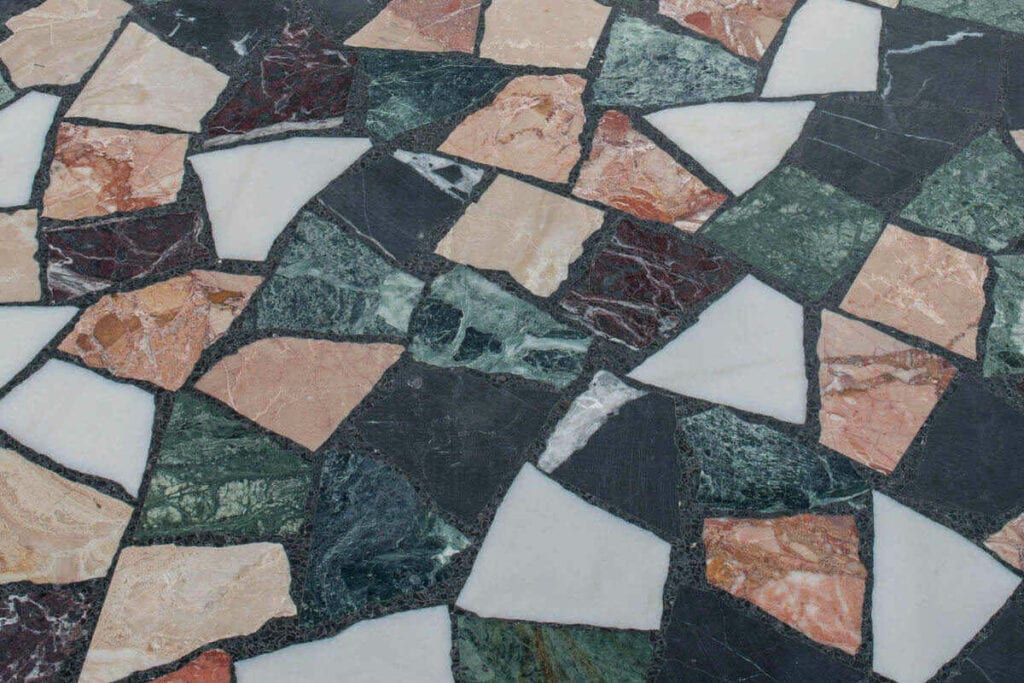
Binder
First of all, decide on the binder material, because a lot of the properties of the final design are determined by the binding agent, which can be either cement or resin.
Terrazzo-Cement
Cement is the traditional material used for terrazzo, and in the EU, the standards of the material are often determined around this type of terrazzo.
It’s extremely durable, can withstand any weather conditions and does not fade in colour. In terms of installation, it can be applied on surfaces that aren’t covered with damp-proof membranes. That’s why cement is the most commonly used material for exterior applications and areas that are subjected to the heaviest of traffic, such as airports. The ventilated cement-based terrazzo facades, that we provide at InOpera, are made using the latest Fischer technology.
Terrazzo-Resin
Terrazzo-resin, on the other hand, is the most popular choice for indoor application. It consists of 93% marble chipping and just 5-7% of the resin binder.
The tiles are thinner, thus, lighter in weight than terrazzo-cement. Also, it’s resilient to cracks, and when used in conjunction with a flexible-membrane, it can absorb some horizontal concrete cracks or control joint movement.
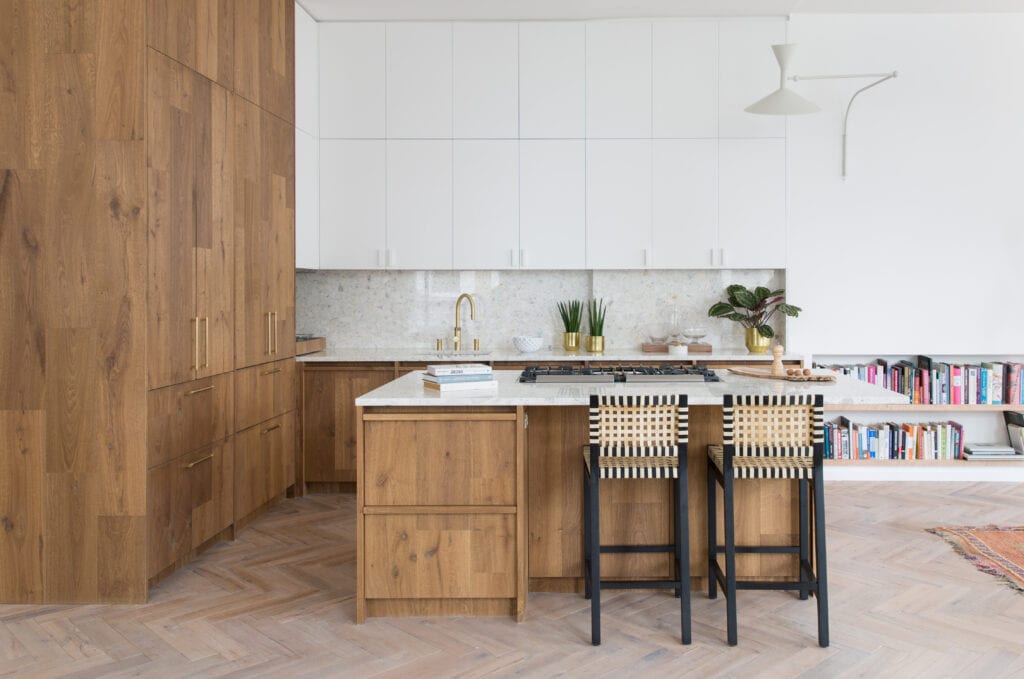
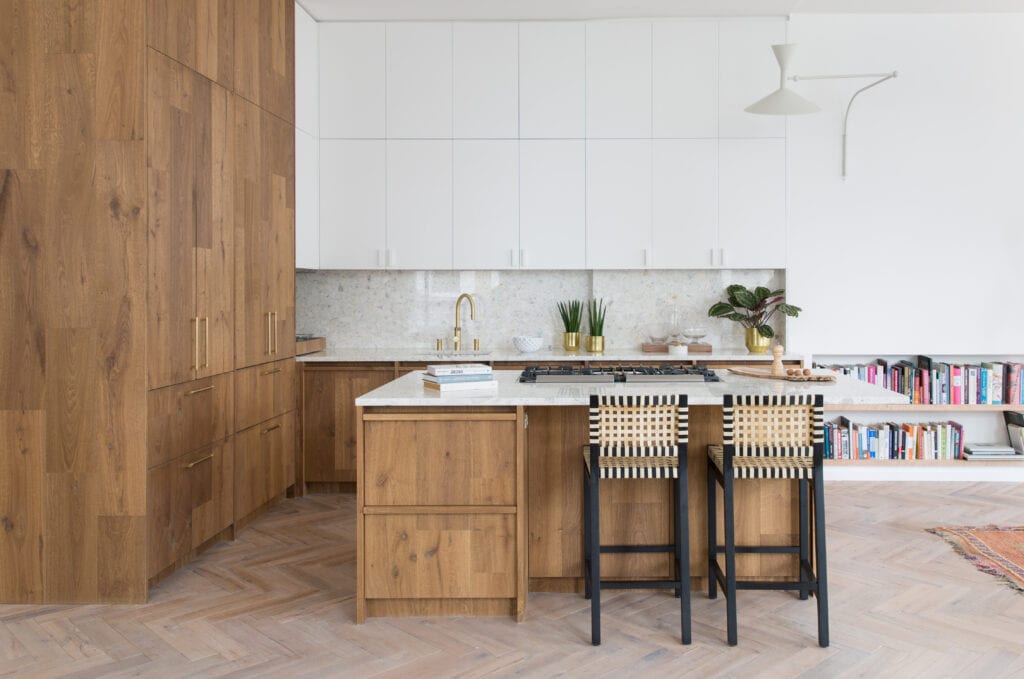
Base colour
Terrazzo’s unique design is the dynamic combination of intricate patterns of natural stone against a plain colour background. The colour of the background or the base is made out of marble dust or other natural oxides. For example, terrazzo with a pink base will be achieved by mixing dust of Rosa Corallo marble.
The base colour can be closely matched to any shade in the RAL chart.
Aggregates and size
The other main component of terrazzo is the aggregate stone.
Marble is the most popular choice from all other materials, but you can get creative here and mix glass, shells, recycled porcelain, and even recycled terrazzo. Recycling aggregate materials can also contribute toward LEED® points.
In terms of the size of the aggregates, it can be as small as 0.8 mm to 30 mm in diameter for cement, and up to 80 mm for resin terrazzo.
Generally, the standard chip sizes are categorized from MK000 to N8 (40 – 50 mm), see the chart below.
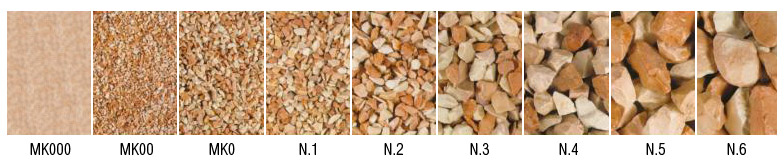
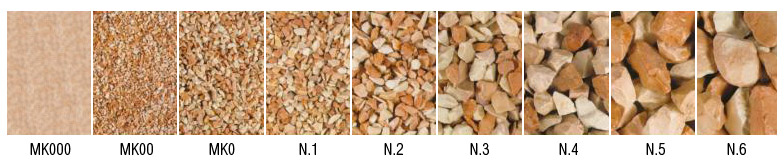
It is worth pointing out that, the bigger the stones are, the thicker the tile needs to be, leading to higher cost. A typical resin terrazzo floor is only 9.5 mm thick, which allows to hold aggregates up to size N3. If the floor needs to be thinner and lighter, terrazzo tile can be as thin as 7.00 mm, meaning only aggregates of size N2 and smaller can be used.
If you want bigger stones for a more rarefied look, cement-based terrazzo is your best choice.
Venetian or Palladiana
Terrazzo which contains stones larger than the standard aggregate size is called Venetian terrazzo. It’s one of the oldest versions of terrazzo made by a method of seminato, which means ‘seeding’ stones.
Palladiana terrazzo, on the other hand is suitable for achieving more paver-like effect with a polished finish, where pieces of marble slabs are used instead of stones.
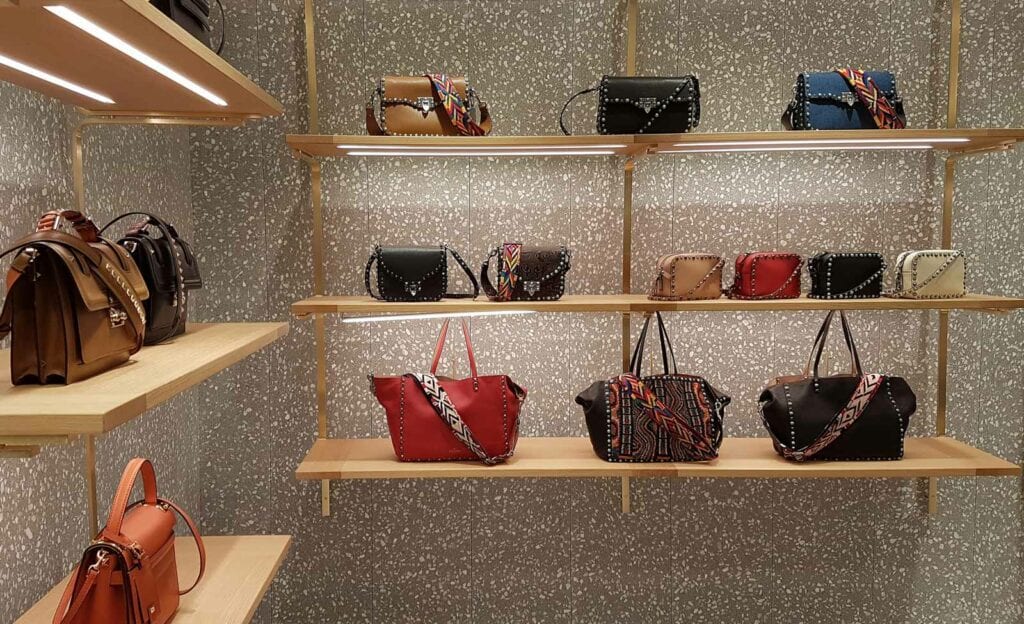
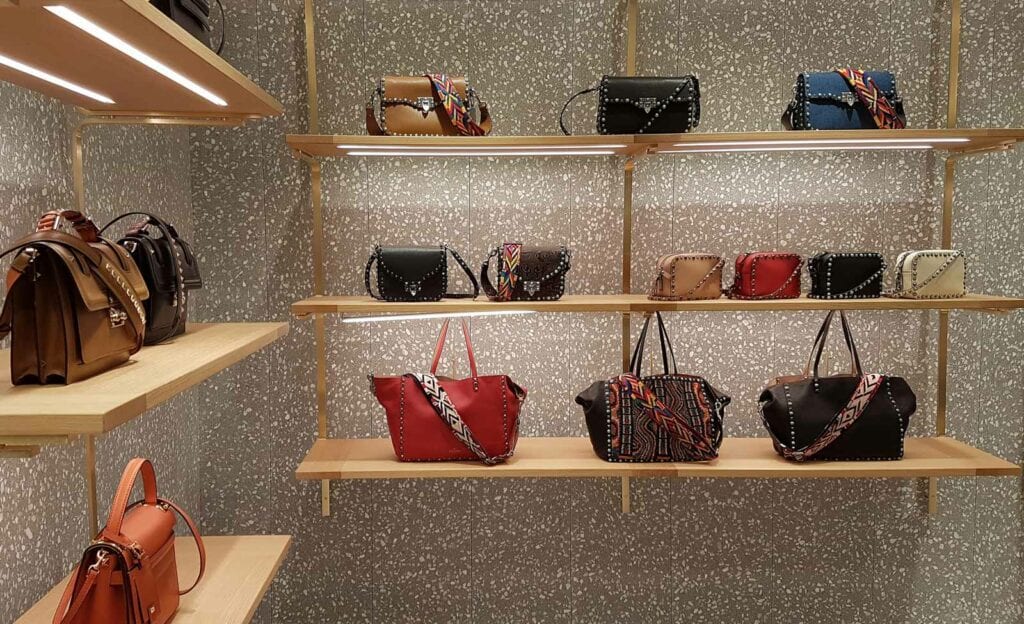
Production method
Once the mixture is ready, it leads us to the production method:
Mechanically pressed tiles
Mechanical method is the fastest and most cost-effective way of producing terrazzo.
The mixture is poured into a block, compressed or vacuumed to give extra strength in the concrete, cured and sliced thinly to be cut into standard-sized tiles.
For cement terrazzo, it takes about a month to cure, and up to two weeks for resin.
The method allows for achieving an even surface throughout the entire block, making it perfect for large-scale projects that require consistency.
Hand cast terrazzo
More intricate terrazzo design will require a traditional hand cast method, where the mixture is poured into bespoke moulds and cured, before being cut to the required size and thickness, ground and polished. This process requires meticulous attention to consistency and colouration, hence, a longer time to produce. As a result, you get a terrazzo tile that is ready for easy installation and looks as if it was installed in-situ.
In-situ
This is the most difficult and oldest method. Once the terrazzo mixture is poured on-site, it is then ground and polished to the required finish. The result is beautiful and smooth flooring, which is not just impressive, in terms of design, but also much easier to maintain than tiled floor joint with grout.
This type of work is difficult, but achievable, done only by specialist installers. Life House by John Pawson was one of the projects we’d supplied materials for, and we’re absolutely stunned by the result.
In general, from our perspective, the mechanically produced terrazzo offer a practical alternative to projects of any purpose, without compromising the durability and aesthetics. The quality of the products undergoes extensive quality control, following international industry standards.
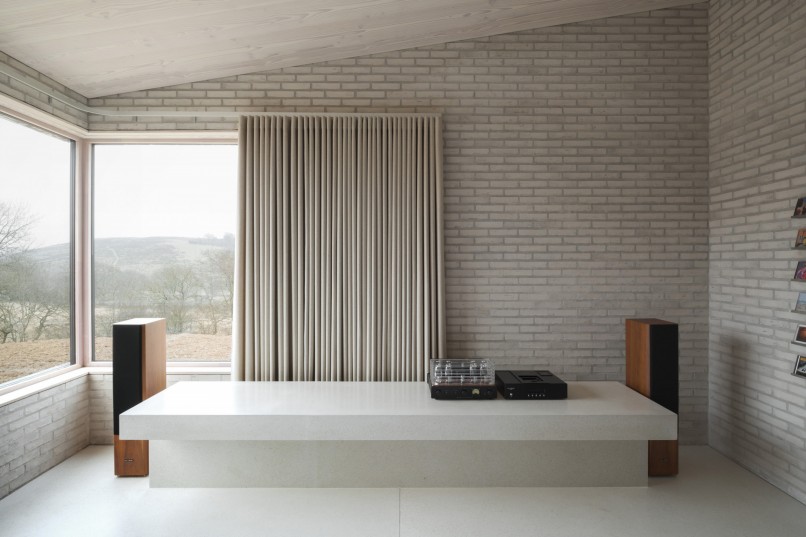
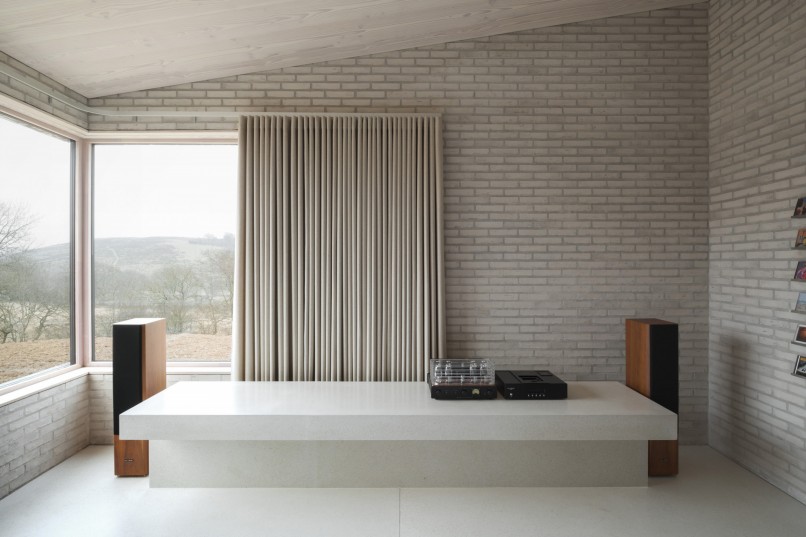
Terrazzo Finishes
Now that we’ve decided on the main components, it is time to settle on the final finish of your surface design. Once terrazzo is cut to size, the surface can have various finishes, from shiny and smooth to bevelled and rough.
Polished
This is when the surface is polished by machine and a protective shiny sealer is applied. It is the glossiest of all finishes and is suitable for low traffic areas.
Honed
This is an anti-slip finish where the surface texture is still smooth and even but the colour is matt and less shiny than in a polished one.
Brushed
Brushed finish, on the other hand, is where you can feel the bevelled shapes of the aggregates. It will still be smooth to the touch, and can even be polished to have a shiny surface.
Sandbalsted
Unlike brushed, it has more porous than bevelled texture. It is highly slip-resistant and is suitable for outdoors and wet areas.
Bush-hammered
This finish, as the name suggests, has a rough distressed feel to it and is commonly used in the exterior.
These are the most common ones, in terms of the finishing surface, but you can also adjust the level of the mechanical and chemical treatment to achieve further textures and patterns.
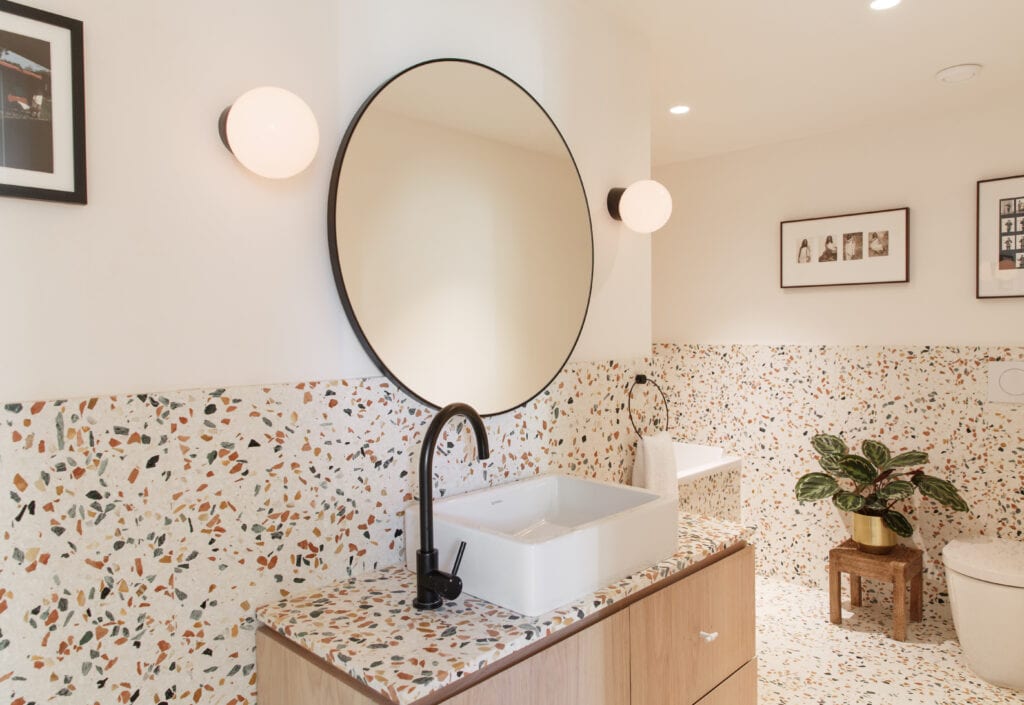
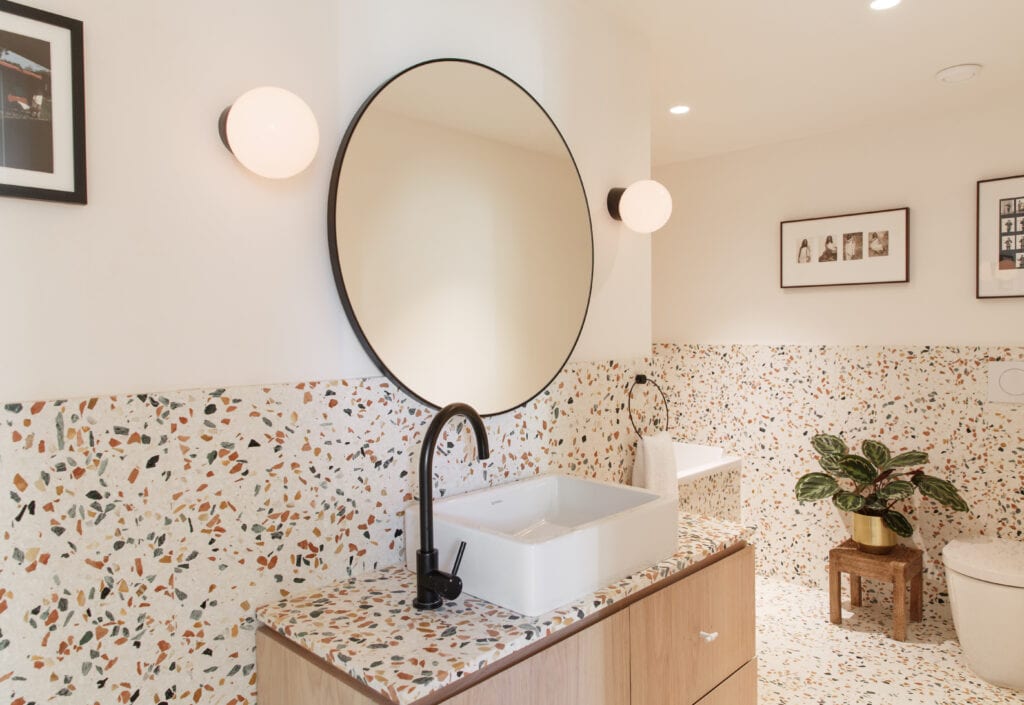
Tile sizes and dividing strips
The cement terrazzo slab can go up to 9 x 3 m and is cut into standard tile size, which is ready for installation. However, the size largely depends on the sub-terrain.
The gap between the tiles is filled with grout which can be closely matched to the colour of the tile body.
However, if you’re going for the in-situ terrazzo, cement terrazzo can only span up to 150 cm in length, and resin terrazzo will cover a much bigger area – for up to 900 cm – before it requires dividing strips.
Dividing strips can be made out of metal, usually, zinc, brass, aluminium, or even high-density black or white plastic to blend in with the tile body colour.
For cement-based terrazzo, dividing strips have to be laid out in grids.
Just remember, you will have to have dividers wherever there are joints in the concrete beneath.
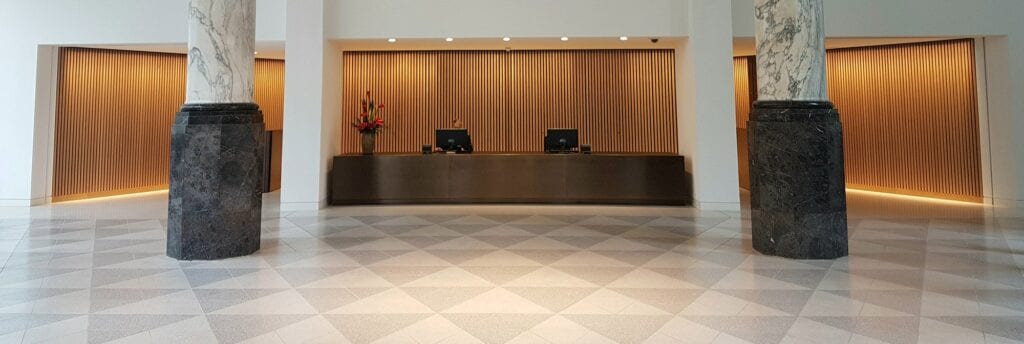
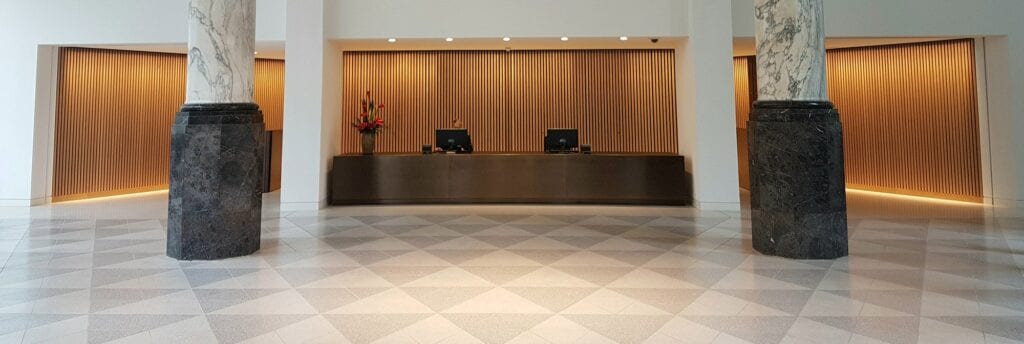
Cost and Planning
In general, terrazzo will require planning, and needs to be installed by trained professionals. Especially, with bespoke terrazzo, colour, size and other properties of the materials have to be initially decided by architects and designers.
We usually prepare a small quantity of bespoke material first, to make sure the end product will match the initial expectations. Once this stage is finalised, our partner factories must then produce terrazzo for the given project.
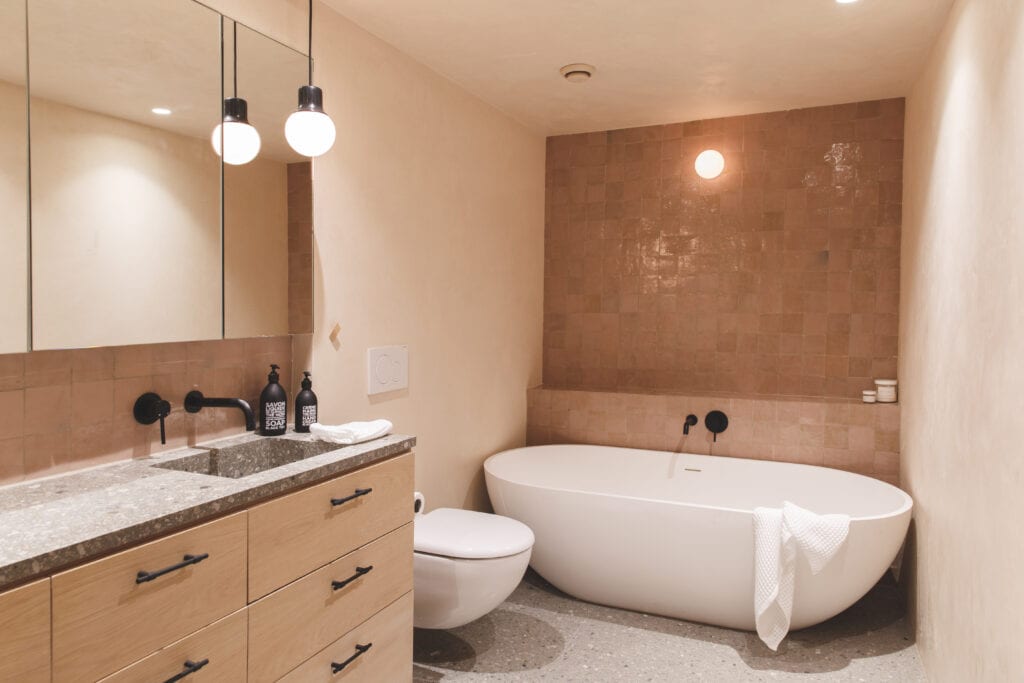
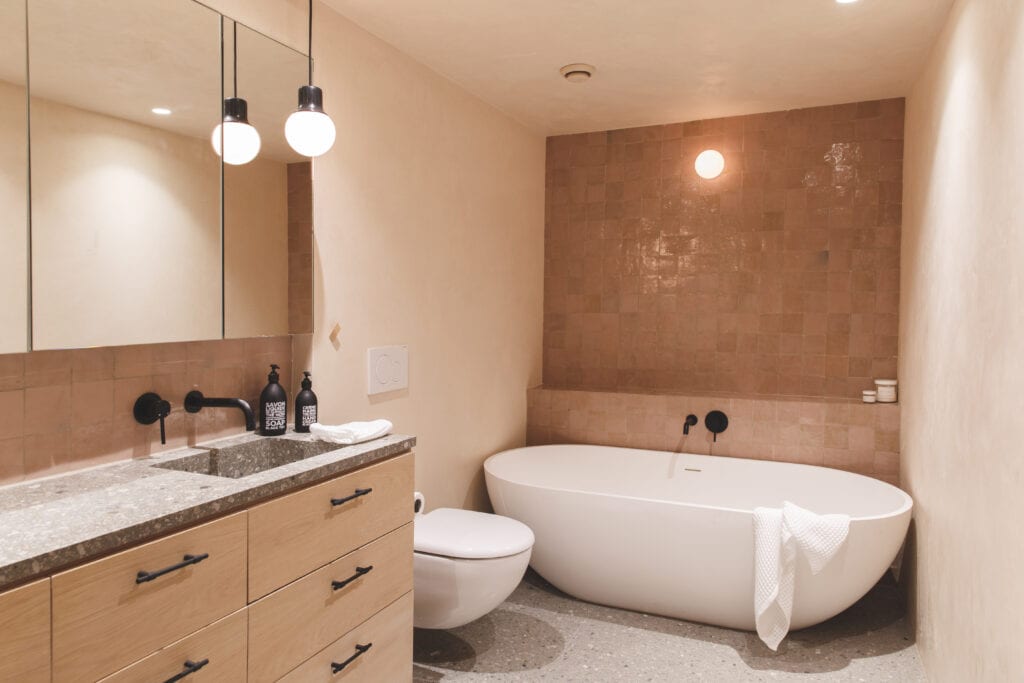
With the standard colour terrazzo, this process is much faster. You can choose a ready sample from any of our products on our website, which will be delivered to your address for free. Once you’re settled with the colour, our technical team will assist you with the quantity and specifications for your project.